Comparing Machine Safeguarding Assessments and Risk Assessments
April 17, 2024 in Machine Safety Blog byEstimated reading time: 7 minutes
Are you uncertain if your machinery can meet modern safety regulations? Using safeguarding or risk assessment methods, you can pinpoint areas where machine protection is lacking and identify potential safety hazards.
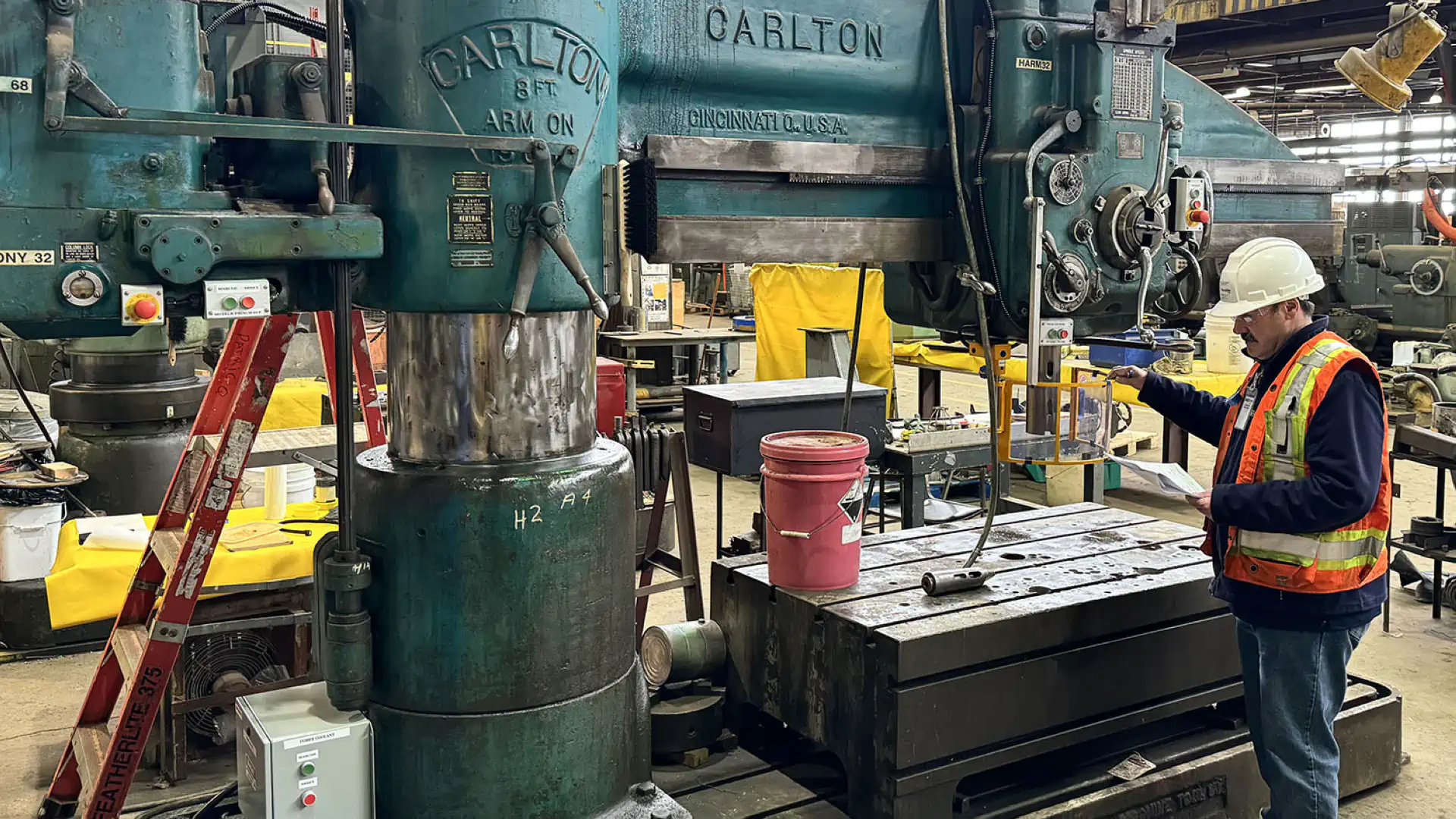
Tons of machines are being set up in companies every day. From small machines like a Home Depot saw to giant machines like automated production lines. While these machines significantly ease our lives, they can also pose substantial risks.
But it’s not always evident how a machine can be dangerous.
Take, for instance, a top-heavy floor standing drill press; it could potentially topple over on someone, causing injury. This risk might not be immediately apparent to many, but securing it to the floor can make the drill press safer.
So then, how can we determine the hazards a machine poses?
What measures can be taken to enhance its safety for users?
Luckily, two key processes facilitate this: conducting a machine safeguarding assessment or performing a machine safety risk assessment. These two tools determine risk and establish what can be done to alleviate it.
Machine Safeguarding Assessments
A machine safeguarding assessment checks whether safeguarding is effectively implemented and operational on machinery and equipment. In other words, a safety assessment checks if a machine has all the standard safety guarding installed and works correctly.
These safeguarding assessments or machine inspections aim to identify non-compliance with regulatory standards and can be performed using a checklist.
A machine safeguarding assessment is best used on conventional machines. However, it can also be performed on machine parts such as motors and belt drives. A drill press is a great example of a machine that could benefit from one.
Look at the following sample checklist. It’s a safeguarding assessment of a drill press, a machine found in almost all metal workshops.
✓ The drill chuck and spindle: Do they have a safety shield?
✓ If so, is the safety shield interlocked?
✓ Electrical: Does it have Anti-restart protection?
✓ Is the machine easily isolated from the power source? (LOTO)
✓ Is it bolted to a table or the floor to avoid tipping?
✓ If there is a belt or pulley cover, is it locked closed with a fastener that requires a tool to open
Or, is there a safety interlock switch to prevent operation while open?
If one or more of the questions above were responded to with a “No,” the machine may require additional safeguarding upgrades.
What does the safety assessment process entail?
A safety professional completes a safety assessment and checks over a machine from top to bottom, noting any obvious safety issues. This step can often be done quickly by an expert. Obvious things to check for are things like broken or missing guards, bypassed interlocks, or other safety issues.
Once an assessment has been completed, you will receive a report on improvements to safety deficiencies or a quote that lists the safety upgrades needed to bring each machine up to safety standards.
Who can do a machine safety assessment?
A range of professionals with expertise in machine safety, occupational health, and industrial regulations can perform a machine safety assessment. The choice often depends on the complexity of the machinery, the specific industry, and regulatory requirements. Here are the primary types of professionals who can perform a machine safety assessment:
- In-House Safety Teams
- Third-Party Safety Consultants/Companies
- Certified Safety Professionals (CSPs)
- Industrial Safety Engineers
- Government or Regulatory Inspectors
- Insurance Risk Assessors
Regardless of who performs the assessment, the individual or team must comprehensively understand the safety standards and regulations applicable to the industry and machinery. Additionally, it is highly beneficial if the person is knowledgeable about the machine’s usage and operation.
They must possess experience in identifying and assessing machinery hazards and understanding the intricacies and potential risks involved. Equally important is their ability to recommend practical and effective safety solutions that can be implemented to mitigate these risks.
Machine Safety Risk Assessment
A risk assessment represents a more advanced machine safety analysis level than a safeguarding evaluation. It involves evaluating the machine’s intended use, identifying associated tasks and hazards, and determining the level of unmitigated risk.
What is risk?
Risk is a measure of the likelihood and consequence of an adverse effect. Risk can affect people and the environment or have financial implications.
A risk assessment demands substantial technical knowledge and resources to be executed correctly and should, therefore, be conducted by professionals. These include safety engineers, Certified Safety Professionals (CSPs), external companies, and specially trained in-house safety teams. Due to its labor-intensive nature, it is often necessary to seek external assistance.
Some companies and jurisdictions require a safety engineer to provide their professional stamp on the completed risk assessment report.
Specific guidelines must be followed, and ANSI B11.0 provides methods for conducting machine risk assessments. In addition, Appendix C of ANSI B11.0 contains a flowchart outlining the steps of the risk assessment process.
Safeguarding Assessment vs. Risk Assessment
Safeguarding Assessment | Risk Assessment | |
Focus | It explicitly targets the safety and adequacy of machine guarding. | Broader evaluation of all potential risks associated with machinery and processes |
Objective | To ensure machine guarding is installed correctly and maintained and to protect workers effectively. | Identify, analyze, and manage risks to prevent accidents and ensure workplace safety. |
Scope | Limited to examining mechanical and electrical safeguards and protective devices on machinery | Includes hazards from machinery, environmental factors, operational procedures, and human factors |
Frequency | It varies, but it should be done regularly. Checks can be done daily or yearly. | Do a risk assessment when a new machine is put into service, when significant changes are performed, or when required. |
Methodology | Inspects physical barriers and protective devices and checks their compliance with safety standards. | It uses tools like risk matrices, FMEA, and HAZOP to assess potential hazards and their impacts. |
Outcome | Recommendations for improving or updating guarding mechanisms, including cost estimates | A comprehensive plan to mitigate identified risks, which may include changes in training, processes, or physical safeguards |
Regulatory Compliance | It focuses on compliance with specific machine guarding standards (e.g., OSHA). | Generally broader, addressing multiple regulatory requirements across safety standards. |
Stakeholders Involved | Typically, it involves safety managers and machine operators. | It may involve a broader range of stakeholders, including safety committees, engineers, and management. |
Key Scenarios for Conducting Risk vs. Safeguarding Assessments
Machine Safeguarding Assessment
- When introducing new equipment, it is important to note that Original Equipment Manufacturers (OEMs) are not required to deliver fully safeguarded machinery. To minimize expenses, manufacturers often exclude expensive safety features. Additionally, OEMs may install low-cost acrylic shields that lack robustness and impact resistance; these should be considered for upgrades to ensure safety. Check out these drill presses for sale that may or may not have a guard.
- After an incident or accident: Unfortunately, I often see a call to action for machine safety only after an accident has already happened. A safeguarding assessment will check if inadequate guarding contributed to the incident. In addition to this, you should do a company-wide machine safeguarding assessment to identify safety issues on all machines.
- Regularly scheduled with a preventative maintenance (PM) program: This will ensure that guarding is in good condition and that operators haven’t bypassed or removed safety guarding. I’m not sure how many countless times I’ve seen electrical interlocks bypassed by operators for convenience.
- Verify periodically every few years if machines meet updated and modern safety standards. Do you have an original 1960s-built lathe that has never been checked? Now would be a good time to do a machine safeguarding assessment and safeguard it to modern safety standards.
Machine Risk Assessment
- Perform a risk assessment before installing new machinery. This is especially important on large or complicated machinery such as robotic cells or production lines. Performing a risk assessment before installing and operating machinery helps us understand all associated risks.
- Whenever there is a change in how machinery or processes are conducted, examples include a retrofit to handle a new product or new hazardous materials usage that introduces new safety protocols.
- After an incident or accident: To identify the cause of the incident and assess all contributing risk factors to prevent future occurrences.
- After an expansion or modification of facilities: Address any new risks introduced by changes in the layout or additional machinery.
- After any significant upgrades to machinery: This includes moving or removing safeguarding or interlocks.
Schedule a call with us today.
Ferndale Safety can help you with:
Please fill out the form below so that one of our safety experts can call you. Alternatively, you can click here to send us a message.